The
steel produced by both BOF and EAF typically follow similar routes after the
molten steel is poured from the furnace. The molten steel is transferred to the
ladle where the metal chemistry is adjusted to meet the final steel product
specifications, which may include adding small amounts of other metal
alloys.
The
steel then proceeds to the continuous caster, which casts the steel into
semi-finished shapes (e.g., slabs, blooms, billets, rounds, and other special
sections). Steel from the continuous caster is processed in rolling mills to
produce the final steel shapes that are sold by the steel mill.
In
most cases, these cast shapes will be cooled and stockpiled for later
introduction into the rolling mill where the final market shape will be
produced. These shapes include coiled strips, rails, and other structural
shapes, as well as sheets and bars. The semi-finished products may be further
processed by using many different steps, such as annealing, hot forming, cold
rolling, heat treating (tempering), pickling, galvanizing, coating, or
painting.
Many
of these steps require additional heating or reheating. The additional heating
or reheating is accomplished using furnaces usually fired with natural gas. The
furnaces are custom designed for the type of steel, the dimensions of the
semi-finished steel pieces, and the desired temperature.
Casting
developments have aimed to reduce the number of process steps involved in
producing the final product. Conventional casting machines may be up to 800m in
length, containing a repeating furnace, roughers and finishers. With the advent
of thin slab casting the number of stages is reduced, typically reducing machine
length to 250m.
Thin
slab casting and direct rolling (TSDR) technologies are nowadays one of the most
promising processing routes to maintain steel as a leading material in
technological applications. Initially, this process was exclusively for the
production of mild steels. As industrial experience and knowledge improved, a
rapid expansion of the range of products took place with higher strength grades
becoming an important part of the overall production. Actually, it is widely
accepted as a route to produce high value grades and it can be considered as a
technology which has reached a high degree of maturity.
Originally,
the Thin Slab based process was developed with the primary goal of reducing the
investment and production costs related to the traditional thick slab process.
The first target achieved, due to design limitations of the casters in the first
generation technologies, was to serve markets with limited requirements (mainly
for low added value commercial applications) and with a productivity around 1
Mtpy (per casting strand) of HRC or less. The 4th-generation of Slab
casters allow production with a variety of added value steel grades that could
not be previously obtained by use of a thick slab caster.
In
the case of thin slab casting, the steel is cast directly to slabs with a
thickness between 1.2 and 2.4 in (30 and 60 mm) instead of slabs with a
thickness of 4.72 to 11.8 in (120 to 300 mm).
The
method involves pouring molten steel into the Tundish at the top of the slab
caster, from a ladle. They are sized with a working volume of min 100 t, which
will deliver the steel at a rate of one ladle every 40 minutes to the caster.
The temperatures of liquid steel in the tundish as well as the steel purity and
chemical composition have a significant impact on the quality of the cast
product.
The
liquid steel passes at a controlled rate into the caster, which is made up of a
water cooled mould in which the outer surface of the steel solidifies. In
general, the slabs leaving the caster are circa 70mm thick, 1000mm wide and
approximately 40m long. These are then cut by the shearer to length. To enable
ease of casting a hydraulic oscillator and electromagnetic brakes are fitted to
control the molten liquid whilst in the mould.
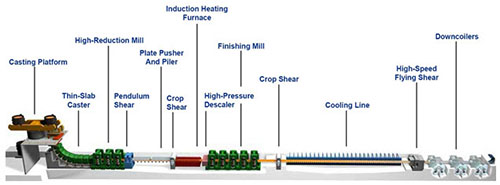
Figure
1: Thin slab caster
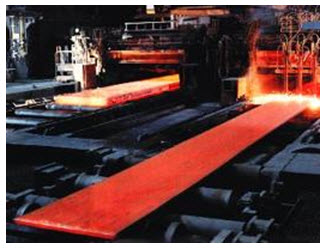
Figure
2: Thin slab casting (in front) in the pilot plant of Mannesmannröhren-